L’aluminium
L’aluminium : naturellement abondant, mais toujours discret
L’aluminium est le métal le plus abondant dans la croûte terrestre. Il représente 8% des matériaux solides à la surface de notre planète.
Pourtant, à l’état naturel, on ne le retrouve jamais tel quel, ce qui explique sa découverte tardive. Il est en effet systématiquement combiné à d’autres éléments sous la forme de minerais divers. Le plus courant est la bauxite, dont on extrait l’alumine.
Pour pouvoir exploiter l’aluminium et toutes ses propriétés, il faut réaliser un travail complexe en plusieurs étapes. L’extraction de l’aluminium de la bauxite demande :
- Des compétences pointues en chimie,
- Une haute maîtrise de la métallurgie,
- Une importante quantité d’énergie, électrique notamment.
Cela explique que l’humanité n’a commencé à connaître, comprendre et exploiter l’aluminium qu’à partir du 19ème siècle.
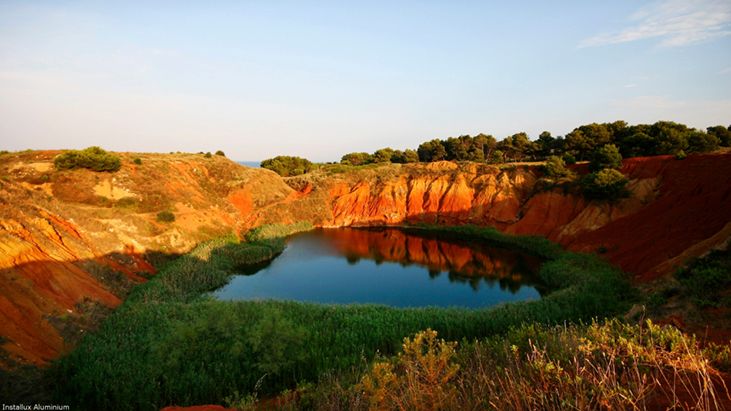
Une histoire récente pour un métal très prometteur
Contrairement à l’or, au cuivre ou au fer, connu depuis l’Antiquité, l’utilisation de l’aluminium est ainsi très récente. Il a fallu attendre les avancées en matière d’industrie minière et de production électrique pour que l’extraction de la bauxite et sa transformation en aluminium soit possible.
À l’époque, c’est la recherche française qui est particulièrement en pointe au sujet de l’extraction et de l’industrialisation de l’aluminium :
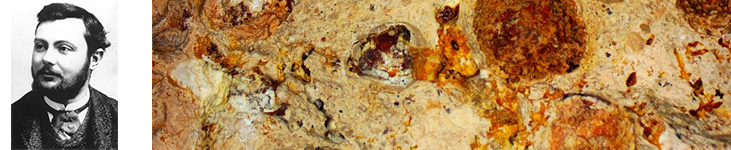
Les qualités de l’aluminium ont très vite été identifiées : légèreté, malléabilité, durabilité, conductivité, etc. Mais, dans un premier temps, son coût de fabrication, très élevé, en faisait un métal précieux, utilisé en joaillerie, au même titre que l’or ou l’argent. Dans les cours royales et impériales d’Europe, il remplaçait parfois l’argent pour la réalisation des couverts utilisés dans les grandes réceptions. Ce n’est qu’à partir de 1886 que son potentiel industriel est exploité pour de nombreuses applications, dans tous les domaines d’activité.
Découvrir les applications de l'aluminium
Extraction et usinage de l’aluminium
Transformer une roche rouge en aluminium utilisé dans toutes nos activités quotidiennes demande un travail colossal. Si l’aluminium est abondamment produit dans le monde, son extraction et son usinage restent complexes, et suivent un processus bien précis.
Une procédure d’extraction en plusieurs étapes
Pour pouvoir utiliser industriellement l’aluminium, il faut l’extraire de son milieu naturel. Contrairement à d’autres métaux, l’aluminium ne se trouve pas à l’état brut dans la nature. Il faut l’extraire de son minerai, la bauxite, en plusieurs étapes.
La bauxite se trouve, à l’état naturel, sous forme de pierres rouges. L’aluminium y est en effet présent sous une forme oxydée. On parle d’oxyde d’aluminium, d’hydroxyde d’aluminium ou, plus simplement, d’alumine. Après avoir récupéré la bauxite, il faut donc lui faire subir une série de transformations :
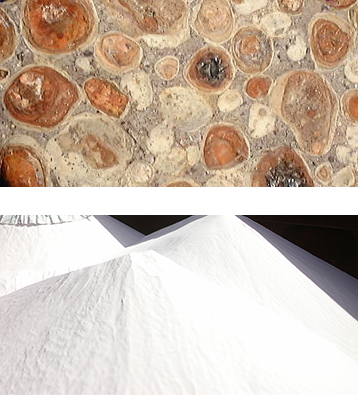
■ La première étape d’extraction consiste à extraire l’alumine contenue dans la bauxite. Cela s’effectue par une procédure chimique où l’on baigne la bauxite dans un bain de soude et de chaux à haute température et haute pression.
■ La partie liquide du mélange est ensuite calcinée pour le déshydrater. On obtient ainsi de l’alumine pure, qui se présente sous la forme d’une poudre blanchâtre.
■ L’alumine est ensuite plongée dans un bain fluoré et à nouveau chauffée à très haute température, pouvant atteindre les 1000°C.
■ Le mélange est soumis à un courant électrique continu extrêmement intense, ce qui lui fait subir une électrolyse. Par ce procédé, l’aluminium se dissocie des autres composés du mélange.
■ L’aluminium liquide se dépose au fond de la cuve, ce qui permet de le récupérer facilement.
Un métal relativement facile à usiner
Après récupération de l’aluminium au fond de la cuve, on profite de son refroidissement pour lui donner une première mise en forme. Ce moulage ne sera pas définitif, mais sera adapté à l’usage qui en sera fait après livraison chez les industriels qui l’utiliseront pour la réalisation de leurs produits définitifs.
En sortie de fonderie, l’aluminium se retrouve principalement sous forme de :
- Plaques,
- Lingots,
- Billes,
- Fil.
Il est ensuite livré sous ces formes dans les usines chargées de l’usiner. Plus tendre et plus léger que la plupart des métaux, l’aluminium s’avère particulièrement facile à mettre en forme. Si son extraction demande de grosses ressources métallurgiques et énergétiques, son usinage est réputé pour être à la fois simple et rapide.
Étant plus tendre que l’acier, par exemple, l’aluminium possède une viscosité plus importante, qui peut être gênante lors de son usinage. Bien vite, cependant, les techniques de découpe, de perçage et de fraisage se sont adaptées. En augmentant la vitesse des manipulations et en utilisant des lubrifiants spécifiques, l’aluminium est finalement un matériau particulièrement simple à travailler. Mieux connaître le cycle de vie de l’aluminium.
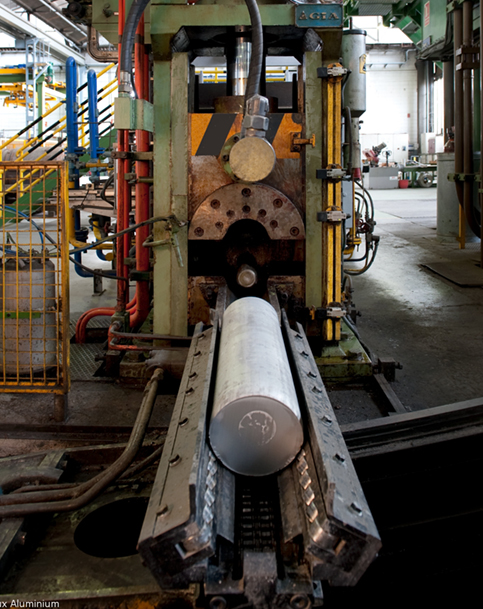
Le saviez-vous ?
Nés tous deux en 1863, sur deux continents différents, les « jumeaux de l’aluminium » Paul Héroult (France) et Charles Martin Hall (États-Unis) ont découvert et breveté l’électrolyse la même année, en 1886. Par la suite liés d’une grande amitié, ils décédèrent tous deux des suites d’une maladie en 1914. Plus de faits et chiffres ➞
Des alliages d’aluminium pour améliorer ses qualités intrinsèques
L’aluminium est réputé pour ses très nombreuses propriétés. Il est à la fois :
- Léger,
- Résistant,
- Insensible à la corrosion,
- Facile à mettre en forme,
- Conducteur sur le plan thermique et électrique,
- Réflecteur, tant pour la lumière que pour la chaleur et les longueurs d’onde infrarouges.
Malheureusement, toutes ces qualités sont parfois incompatibles entre elles. La malléabilité de l’aluminium, qui permet une mise en forme facilité, peut le rendre trop sensible aux déformations suite à un choc, par exemple. De manière générale, certains utilisateurs ont très vite souhaité troquer un peu de sa légèreté et de sa malléabilité contre une plus grande résistance. Et c’est très précisément ce que permettent de faire les alliages.
En mélangeant de l’aluminium à d’autres métaux en très petite quantité, il est possible de lui apporter de nouvelles propriétés physiques. Ou plus généralement, de renforcer certaines de ces qualités intrinsèques. Les alliages d’aluminium les plus courants incorporent ainsi du silicium, du manganèse, du magnésium ou du cuivre. Ces alliages sont parmi les plus simples à travailler. Pour un industriel, cela permet d’obtenir des découpes et des profilés complexes aux propriétés spécifiques, particulièrement résistants et performants.
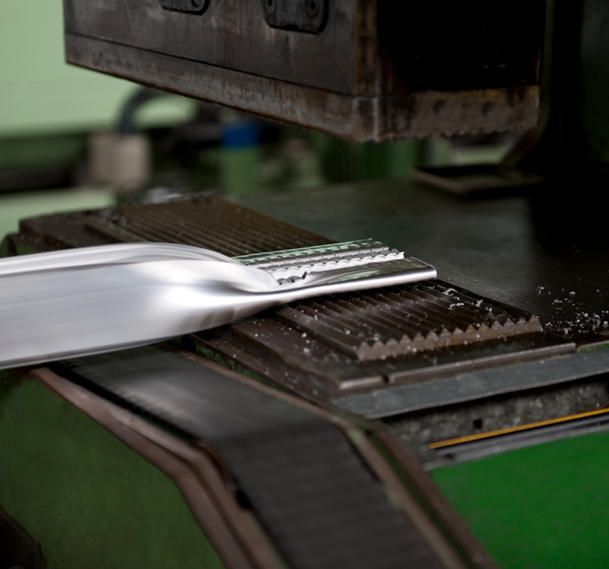
L’omniprésent aluminium
Grâce à tous ces procédés industriels, et à cet incroyable processus de transformation, l’aluminium est devenu progressivement le métal du 20ème siècle, omniprésent dans nos vies.
Aujourd’hui, c’est un métal tout bonnement incontournable dans de nombreux secteurs industriels, mais aussi dans notre vie quotidienne.
Industrie aéronautique et spatiale : léger et résistant, l’aluminium est idéal pour la conception d’objets volants. C’est le matériau de base pour la conception des avions civils et militaires, des lanceurs spatiaux, des sondes interplanétaires et des satellites.
Construction navale : très résistant à la corrosion, même en milieu salin, l’aluminium est très apprécié pour réaliser les coques de navires légers et rapides, mais aussi pour les superstructures des plus gros navires civils et militaires.
Automobile et transport terrestre : l’utilisation de l’aluminium a permis de réduire drastiquement le poids des voitures, permettant d’augmenter leur niveau de sécurité tout en diminuant leur consommation de carburant. Il a également révolutionné le monde des deux-roues, et des chemins de fer.
Médical : parfaitement imperméable, il est utilisé dans les emballages de la plupart des médicaments. Il entre également dans la fabrication de très nombreux équipements médicaux.
BTP : l’aluminium est utilisé abondamment pour la construction de structures légères et aériennes, comme les vérandas, et autres baies vitrées. Retrouvez toutes les innovations de l’aluminium.