Aluminium
Aluminium: naturally abundant, but always discreet
Aluminium is the most abundant metal in the earth’s crust. It represents 8% of the solid materials on the surface of our planet.
And yet it is never found as such in a natural state, which explains why it was discovered only relatively recently. It is systematically combined with other elements in the form of various ores. The most common one is bauxite, from which alumina is extracted.
A complex process in many stages is required before one can exploit aluminium and all its properties. Extracting aluminium from bauxite requires:
- Specialized expertise in chemistry,
- A good command of metallurgy,
- A large quantity of energy, electrical in particular.
This explains why mankind only began finding out about, understanding and exploiting aluminium in the 19th century.
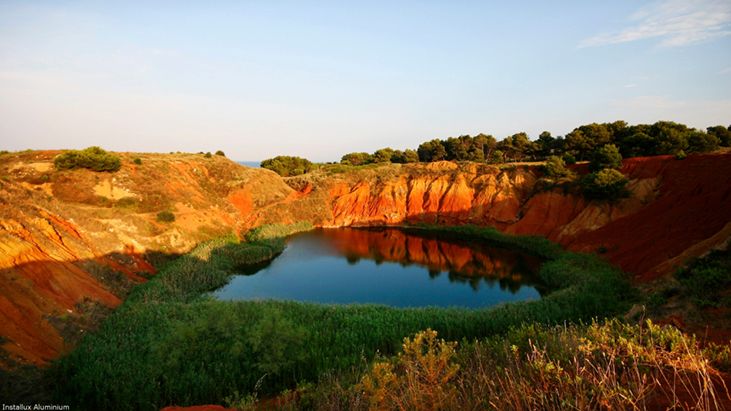
A recent history for a very promising metal
Unlike gold, copper or iron, which have been known since antiquity, the use of aluminium is very recent. Only advances in the mining industry and in power generation made it possible to extract bauxite and convert it into aluminium.
At the time, French research was particularly advanced regarding the extraction and industrialization of aluminium:
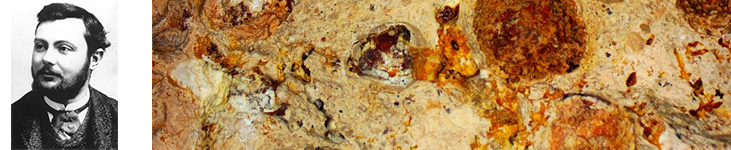
The following qualities of aluminium were very quickly identified: lightness, malleability, durability, conductivity, etc. But at first its very high cost of production made it a precious metal, only used in jewellery, in the same way as gold or silver. In the royal and imperial courts of Europe, it sometimes replaced silver in the cutlery used for important receptions. It was only in 1886 that its industrial potential started being exploited for numerous applications, in all fields of activity.
Discover the applications of aluminium
Aluminium extraction and machining
Converting a red rock into the aluminium we use in all our day-to-day activities requires a colossal amount of work. While aluminium is produced abundantly throughout the world, its extraction and machining remain complex, requiring a very specific process.
A multistage extraction procedure
To be able to use aluminium industrially, it must first be extracted from its natural environment. Unlike other metals, aluminium is not found in an unrefined state in nature. It needs to be extracted from its ore, bauxite, in stages.
Bauxite is found in a natural state in the form of red stones. The aluminium it contains is in oxidized form. This is called aluminium oxide, aluminium hydroxide or simply alumina. After the bauxite is mined, it then has to undergo a series of transformations:
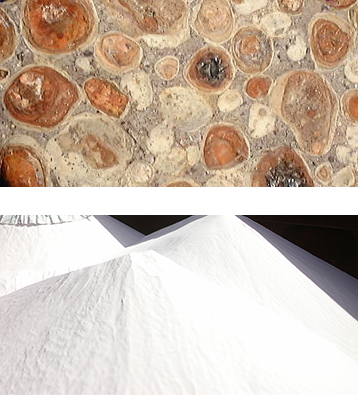
■ The first stage consists in extracting the alumina from the bauxite. This is done chemically, by soaking the bauxite in a bath of soda and lime at high temperature and high pressure.
■ The liquid part of the mixture is then calcined to dehydrate it. This leaves pure alumina, in the form of a whitish powder.
■ The alumina is then poured into a fluorinated bath and again heated at a very high temperature of up to 1000°C.
■ The mixture is then subjected to an extremely intense direct electric current, a process called electrolysis. This process separates the aluminium from the other compounds in the mixture.
■ The liquid aluminium is deposited on the bottom of the pot, from where it can easily be recovered.
A relatively easy metal to machine
After the aluminium is collected from the bottom of the pot, we use its cooling stage to give it an initial form. This moulding is not definitive, but is adapted to the use that will be made of it after delivery to manufacturers, who use it to make their finished products.
When it leaves the smelting plant, aluminium is mainly in the form of:
- Plates,
- Ingots,
- Pellets,
- Wire.
It is then delivered in these forms to the plants that machine it. Softer and lighter than most metals, aluminium proves particularly easy to form. While its extraction requires a great deal of metallurgic and energy resources, its machining is well-known as being both simple and rapid.
Softer than steel for instance, aluminium is more viscous, which can be problematic when machining it. But cutting, drilling and milling techniques quickly adapted to this property. By increasing the speed of manipulations and using special lubricants, aluminium is ultimately a very simple material to work with. Learn more about the life cycle of aluminium.
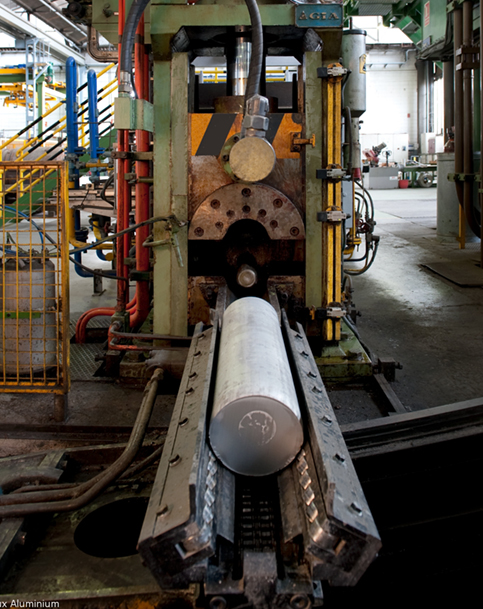
Did you know?
Both born in 1863, on two different continents, the “aluminium twins” Paul Héroult (France) and Charles Martin Hall (United States) discovered and patented electrolysis in the same year, in 1886. Subsequently great friends, they both died after a long illness in 1914. More facts and figures
Aluminium alloys to improve its intrinsic qualities
Aluminium is reputed for its numerous properties. It is at once:
- Light,
- Strong,
- Corrosion-proof,
- Easy to form,
- Conductive, both thermally and electrically,
- Reflective, for light, heat and infrared wavelengths.
Unfortunately, not all these qualities are compatible with one another. The malleability of aluminium, which facilitates its forming, can make it too sensitive to deformation further to an impact, for instance. Generally speaking, certain users very quickly wished to trade a little of its lightness and malleability for greater strength. And that is precisely the role of alloys.
By mixing aluminium with other metals in very small quantities, we can give it new physical properties. Or more generally reinforce some of its intrinsic qualities.
The most common aluminium alloys include silicon, manganese, magnesium or copper. These alloys are some of the easiest to work. This allows manufacturers to make complex cuts and sections with specific properties, which are particularly strong and efficient.
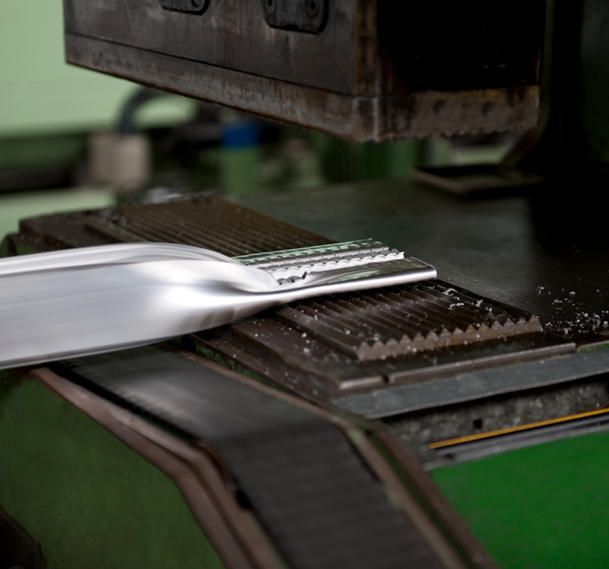
Omnipresent aluminium
Thanks to all these industrial processes and this incredible conversion process, aluminium has gradually become the metal of the 20th century, omnipresent in our lives.
In this day and age it is quite simply an indispensable metal in many industrial sectors, as it is in our everyday life.
Aeronautical and aerospace industry: light and strong, aluminium is the ideal metal for designing flying objects. It is the basic material for designing civil and military aircraft, space launch vehicles, interplanetary probes and satellites.
Shipbuilding: very corrosion-resistant, even in saline environments, aluminium is very valued for making the hulls of light and rapid ships, as well as the superstructures of the largest civil and military ships.
Automobile and inland transport: aluminium has drastically reduced the weight of cars, increasing their safety level while reducing their fuel consumption. It has also revolutionized the world of two-wheeled vehicles and railways.
Medical: totally impermeable, it is used in the packaging of most medicines. It is also used in the manufacture of a great many medical devices.
Building and public works: aluminium is used abundantly in the construction of lightweight and overhead structures such as conservatories, bay windows and other features. Learn more about the innovations of aluminium.